In today’s interconnected industrial landscape, managing complex networks effectively is crucial to operational efficiency and cost-effectiveness. MIMOSA (Maintenance, Information, Modeling, and Optimization for System Applications) is a powerful framework that facilitates seamless integration, data management, and predictive maintenance across industrial networks. But how can MIMOSA be practically implemented in an industrial environment? In this guide, we’ll walk you through the key steps for successfully implementing MIMOSA in your industrial network, covering everything from initial planning to overcoming common challenges and measuring success.
-
Introduction: What is MIMOSA and Why is It Important for Industrial Networks?
MIMOSA is an open standard developed to improve the management of complex industrial networks, particularly in the areas of asset management and maintenance. It provides a unified framework for integrating data from various systems, such as sensors, monitoring tools, and enterprise software, enabling companies to manage assets and operations more efficiently.
In industrial environments, where machinery, equipment, and infrastructure are critical to daily operations, MIMOSA ensures that everything works together seamlessly. It reduces downtime, enhances asset management, and enables predictive maintenance, all of which contribute to smoother, more cost-effective operations.
The importance of MIMOSA lies in its ability to break down the silos between different systems, making the data from disparate sources more accessible and actionable. The Practical Implementation Guide for MIMOSA in Industrial Networks will help you understand how to make the most of this powerful framework.
-
Understanding the Key Components of MIMOSA for Industrial Networks
Before diving into the practical implementation of MIMOSA, it’s essential to understand the key components that make it so effective in industrial networks.
- Data Models: MIMOSA uses standard data models to represent equipment, systems, and assets. These models help ensure that data from various devices and systems can be integrated and understood in a consistent way.
Asset Management: MIMOSA offers frameworks for tracking and managing the health of assets throughout their lifecycle. This includes monitoring performance, predicting failures, and making decisions regarding maintenance and repairs. The Practical Implementation Guide for MIMOSA in Industrial Networks can help organizations effectively set up asset management systems that integrate with existing infrastructure for optimal results.
Predictive Maintenance: One of MIMOSA’s strongest features is its ability to support predictive maintenance, which uses data and analytics to predict when an asset might fail. This enables organizations to perform maintenance just in time, reducing downtime and increasing asset lifespan. Following The Practical Implementation Guide for MIMOSA in Industrial Networks ensures that the predictive maintenance process is aligned with industry best practices and tailored to specific organizational needs.
- Interoperability: MIMOSA is designed to work seamlessly across different systems, ensuring that data can flow freely between various platforms (e.g., sensors, ERP systems, maintenance tools). To achieve true interoperability, The Practical Implementation Guide for MIMOSA in Industrial Networks provides step-by-step instructions for integrating disparate systems into a unified, effective network
-
Step-by-Step Guide to Implementing MIMOSA in Industrial Networks
Now that we understand the key components, let’s break down The Practical Implementation Guide for MIMOSA in Industrial Networks to help you put this framework into action:
-
Planning and Preparing Your Network
The first step in any MIMOSA implementation is to understand your current network’s structure and needs. Conduct a thorough audit of your existing systems, assets, and maintenance processes. Identify the gaps and areas where MIMOSA can provide the most value. Define clear objectives for what you hope to achieve (e.g., reducing downtime, improving predictive maintenance).
-
Setting Up the Infrastructure
MIMOSA requires a solid infrastructure to function effectively. This may involve upgrading your existing network architecture to ensure that all systems can communicate and share data. You’ll need to implement compatible data collection and monitoring tools (e.g., sensors, condition monitoring systems) to feed into the MIMOSA framework. Make sure to choose systems that support open standards and ensure interoperability with the MIMOSA framework.
- Integration with Existing Systems
Integrating MIMOSA into your network means connecting it to your existing data sources and platforms. This may involve using middleware or custom-built connectors to ensure smooth data flow between systems. Consider collaborating with IT and network specialists to manage this process efficiently. The Practical Implementation Guide for MIMOSA in Industrial Networks can offer valuable insights on how to integrate these components effectively. Data models and standards defined by MIMOSA should be mapped to your existing assets and systems. This integration ensures that data can be interpreted correctly and used in asset management and maintenance decision-making, following the principles outlined in The Practical Implementation Guide for MIMOSA in Industrial Networks.
- Training and Knowledge Transfer
Implementing MIMOSA is not just about installing new systems—it’s about empowering your team to leverage these tools effectively. Training employees on how to use the new tools, interpret data, and apply predictive maintenance techniques is crucial. Invest in training programs and ensure that your staff is familiar with the MIMOSA framework and its functionalities. This will maximize the effectiveness of the system and ensure smoother day-to-day operations.
-
Common Challenges During MIMOSA Implementation and How to Overcome Them
While MIMOSA provides significant advantages, there are some challenges to be aware of during its implementation:
- Integration Issues: Since MIMOSA is built to integrate with a variety of systems, challenges can arise when trying to connect legacy equipment or outdated software. To address this, you may need to upgrade older systems or invest in integration tools that bridge the gap between new and old technologies.
- Employee Resistance to Change: Implementing a new system often meets with resistance from employees who are used to older ways of doing things. To mitigate this, involve key stakeholders early in the process and provide comprehensive training.
- Data Overload: With MIMOSA’s ability to collect vast amounts of data, there can be a risk of data overload. This can be managed by setting up clear data governance protocols and focusing on the most critical metrics for your operations.
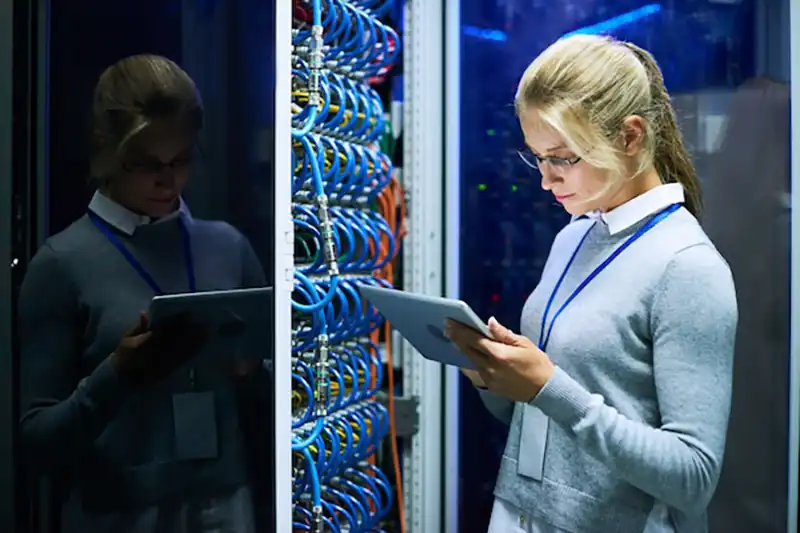
-
Measuring Success: How to Evaluate the Effectiveness of MIMOSA in Your Network
Once MIMOSA has been implemented, it’s important to track its effectiveness. Key performance indicators (KPIs) can help you measure success and identify areas for improvement.
- Downtime Reduction: One of the primary benefits of MIMOSA is the reduction in unplanned downtime. Track the amount of downtime before and after implementation to assess the system’s impact.
- Cost Savings: Measure the cost savings from predictive maintenance and reduced failure rates. MIMOSA’s ability to help you perform maintenance just in time can significantly reduce costs related to repairs and emergency shutdowns.
- Asset Performance: Track the performance of critical assets over time. Are they lasting longer? Are you able to detect failures before they happen? These metrics will help evaluate the overall impact of MIMOSA on your asset management strategy.
Q&A Section:
Q: What industries can benefit from implementing MIMOSA?
A: MIMOSA is particularly useful in industries like manufacturing, energy, utilities, and transportation, where complex industrial networks and critical assets require constant monitoring and maintenance.
Q: How long does it take to implement MIMOSA in an industrial network?
A: Implementation time can vary depending on the size and complexity of your network. On average, it may take several months to fully integrate MIMOSA, including system setup, testing, and employee training.
Q: Do I need specialized staff to implement MIMOSA?
A: While MIMOSA is designed to be user-friendly, having IT professionals, network engineers, and maintenance specialists involved in the implementation process can ensure a smoother transition.
Q: What is the cost of implementing MIMOSA in an industrial network?
A: The cost depends on the scale of your network and the systems you already have in place. Factors like the need for system upgrades, integration tools, and employee training will influence the overall cost.
Conclusion:
This practical guide outlines The Practical Implementation Guide for MIMOSA in Industrial Networks. By following these key steps and addressing potential challenges, organizations can successfully implement MIMOSA to optimize network management and asset performance. With a structured approach, clear objectives, and effective training, MIMOSA can significantly enhance the efficiency and cost-effectiveness of your industrial network.
For further resources and support, visit wizland.