Introduction:
Predictive maintenance has become a key strategy in modern industries, helping organizations prevent unexpected breakdowns and maximize the lifespan of their assets. But how do organizations achieve the level of insight and precision needed for predictive maintenance? One of the most effective solutions lies in utilizing MIMOSA standards for predictive maintenance with OSA-CBM (Open Systems Architecture for Condition-Based Maintenance). Let’s explore how this powerful combination is transforming maintenance practices across industries.
-
Introduction to MIMOSA and OSA-CBM
MIMOSA, which stands for Maintenance, Information, Modeling, and Optimization for System Applications, provides a standardized framework for managing and exchanging asset management data. It focuses on ensuring that different systems and tools can communicate effectively and share maintenance data in a consistent format.
On the other hand, OSA-CBM is an open architecture designed specifically for condition-based maintenance. It focuses on continuously monitoring the health of equipment and assets, triggering maintenance only when conditions indicate the need for intervention. The goal of OSA-CBM is to reduce unnecessary maintenance activities while preventing unscheduled downtime.
When combined, utilizing MIMOSA standards for predictive maintenance with OSA-CBM offers a robust approach to predictive maintenance, ensuring that asset data is consistent, actionable, and timely.
-
What are MIMOSA Standards and How Do They Benefit Predictive Maintenance?
MIMOSA standards provide a unified approach to asset management data, ensuring that information is structured and shared in a way that is easy to use across different systems. In predictive maintenance, the need for accurate and up-to-date data is paramount. Without proper standards, data from various sources could be inconsistent, leading to confusion and inefficiency.
By utilizing MIMOSA standards for predictive maintenance with OSA-CBM, organizations can ensure that data from sensors, maintenance records, and equipment diagnostics can be integrated and analyzed effectively. This data standardization allows predictive maintenance systems to detect patterns, predict failures, and recommend preventive actions with greater accuracy.
Additionally, MIMOSA enables better collaboration across teams by using a common language for asset management, improving the overall coordination between maintenance, operations, and engineering teams.
-
OSA-CBM: The Core of Predictive Maintenance
OSA-CBM, or Condition-Based Monitoring, forms the foundation of predictive maintenance. By continuously monitoring the health of assets using sensors and other diagnostic tools, OSA-CBM allows companies to track the real-time performance of their equipment. It identifies early signs of wear and tear, allowing maintenance teams to intervene before a failure occurs.
This proactive approach is far more cost-effective than traditional reactive maintenance or even scheduled preventive maintenance, which may lead to unnecessary repairs. By focusing only on equipment that needs attention, OSA-CBM optimizes resources and minimizes downtime.
OSA-CBM relies heavily on the data provided by utilizing MIMOSA standards for predictive maintenance with OSA-CBM to ensure that the condition monitoring data is consistent, reliable, and actionable. With OSA-CBM, businesses can avoid the risk of downtime caused by unplanned failures while extending the life of their assets.
-
How MIMOSA Standards and OSA-CBM Work Together for Better Predictive Maintenance
When utilizing MIMOSA standards for predictive maintenance with OSA-CBM, the result is a highly efficient predictive maintenance strategy. MIMOSA ensures that data is organized and standardized, making it easier for OSA-CBM systems to interpret and act upon that information.
For instance, a turbine in a power plant might have several sensors monitoring factors like vibration, temperature, and pressure. MIMOSA ensures that this sensor data is formatted consistently, so that OSA-CBM systems can detect any abnormalities or trends that might indicate a potential failure. Once a warning is triggered, predictive analytics can forecast the time until failure, allowing the maintenance team to schedule repairs at the optimal time, avoiding unplanned downtime.
This integration enables organizations to move from reactive to predictive maintenance, improving asset management, extending equipment life, and reducing maintenance costs.
-
Key Benefits of Utilizing MIMOSA Standards for Predictive Maintenance
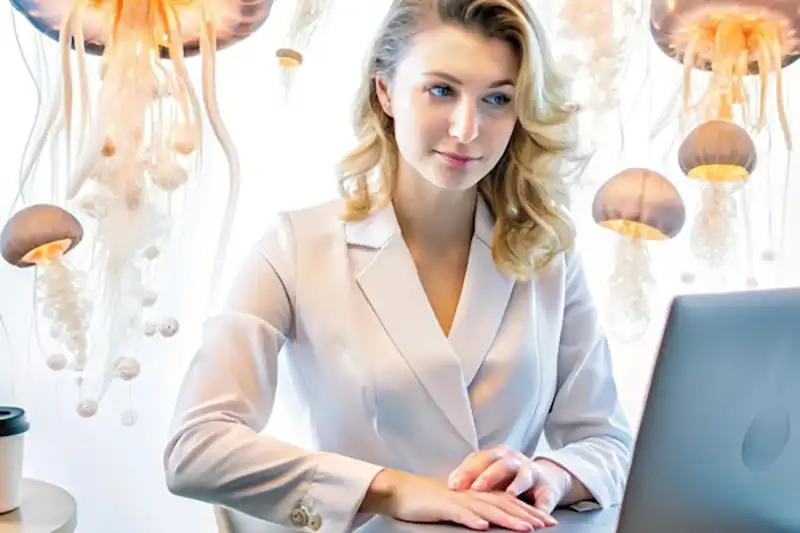
Utilizing MIMOSA standards for predictive maintenance with OSA-CBM comes with a host of benefits:
- Reduced Downtime: With predictive maintenance powered by OSA-CBM and MIMOSA standards, organizations can identify issues before they cause equipment failure, reducing unplanned downtime significantly.
- Cost Savings: By minimizing unnecessary maintenance activities and only performing maintenance when needed, companies save on labor, parts, and overall maintenance costs.
- Improved Efficiency: With accurate, real-time data, organizations can optimize maintenance schedules, allocate resources more effectively, and improve overall operational efficiency.
- Long-Term Asset Management: Proper use of predictive maintenance ensures that assets are maintained at their peak performance for longer, increasing their lifespan and reducing the total cost of ownership.
- Better Decision Making: MIMOSA standards provide a reliable data foundation, enabling organizations to make informed decisions based on accurate and up-to-date information.
Q&A Section:
Q: How can MIMOSA and OSA-CBM improve maintenance reliability?
A: By ensuring standardized and consistent data, MIMOSA improves the accuracy of predictive maintenance systems, while OSA-CBM uses that data to make informed decisions about when maintenance is required, improving overall reliability.
Q: What industries benefit most from utilizing MIMOSA and OSA-CBM?
A: Industries such as manufacturing, energy, transportation, and utilities that rely on high-value assets and cannot afford downtime benefit greatly from predictive maintenance using MIMOSA and OSA-CBM.
Q: Can OSA-CBM be used independently, or does it need MIMOSA standards?
A: While OSA-CBM can function independently, utilizing MIMOSA standards for predictive maintenance with OSA-CBM significantly enhances its effectiveness by ensuring that data from different systems is standardized and easy to interpret.
Q: What challenges might companies face when implementing MIMOSA and OSA-CBM?
A: The main challenges include the initial setup of sensors and data collection systems, ensuring compatibility between existing equipment and MIMOSA standards, and training personnel to use new predictive maintenance tools effectively.
Conclusion:
In conclusion, utilizing MIMOSA standards for predictive maintenance with OSA-CBM offers a highly effective approach to improving asset management and minimizing downtime. By ensuring that maintenance data is standardized, consistent, and actionable, MIMOSA standards enable OSA-CBM to predict failures with greater accuracy and efficiency. As a result, businesses can extend the life of their assets, reduce maintenance costs, and optimize their operations.
For more insights into predictive maintenance and asset management, visit us at wizland.